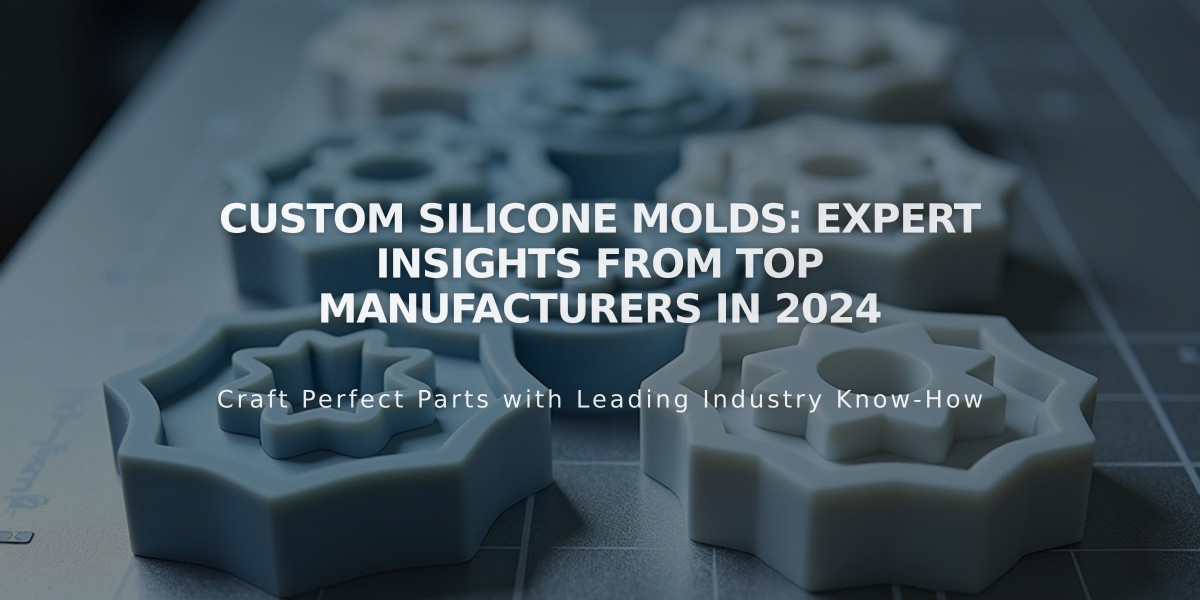
Custom Silicone Molds: Expert Insights from Top Manufacturers in 2024
Custom silicone molds represent modern manufacturing's cutting edge, offering unmatched precision and flexibility across various industries. Their adaptability and performance make them essential for complex production needs.
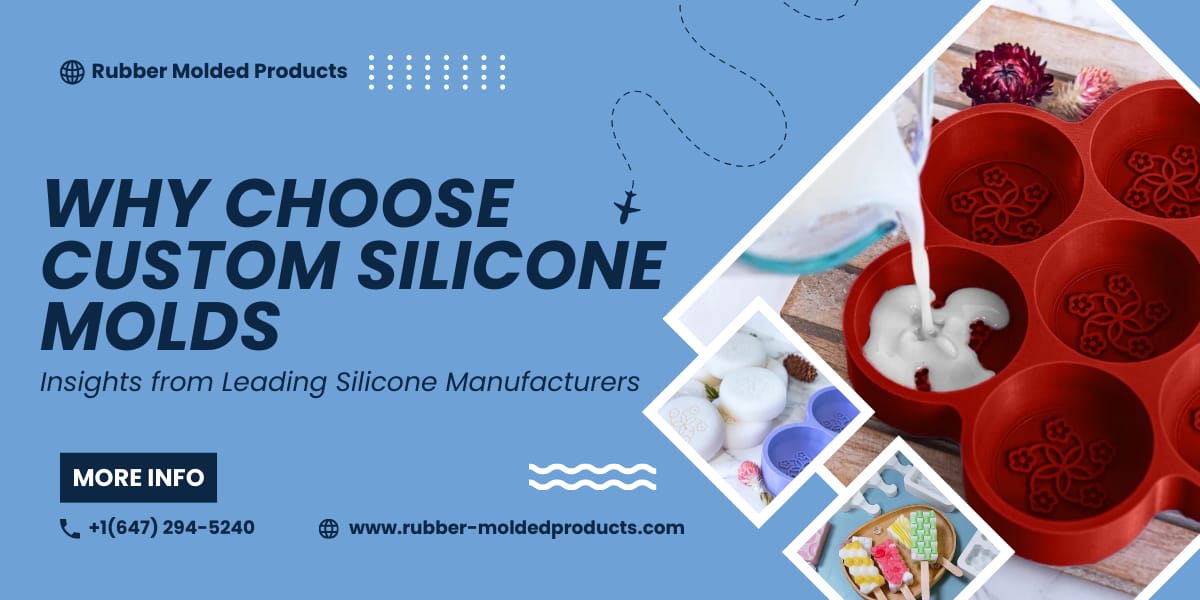
Pouring white silicone into molds
Technical Advantages:
- Superior temperature resistance (-50°C to +200°C)
- Excellent chemical resistance
- High durability and flexibility
- Precise detail reproduction
- Cost-effective for multiple uses
- Non-toxic and food-grade options available
Industry Applications:
- Medical devices and equipment
- Automotive components
- Aerospace parts
- Consumer electronics
- Food production
- Industrial machinery
Manufacturing Precision Techniques:
- Injection molding
- Compression molding
- Transfer molding
- Liquid silicone rubber (LSR) molding
- Advanced surface finishing
Material Selection Considerations:
- Operating temperature range
- Chemical exposure requirements
- Mechanical stress tolerance
- Regulatory compliance needs
- Cost-effectiveness
- Production volume requirements
Quality Assurance Measures:
- ISO certification compliance
- Material testing protocols
- Dimensional accuracy verification
- Surface finish inspection
- Operational performance testing
Emerging Technologies:
- 3D printing integration
- Computational modeling
- Advanced simulation capabilities
- Machine learning optimization
- Automated quality control
Sustainability Initiatives:
- Recyclable material options
- Energy-efficient production
- Waste reduction strategies
- Bio-based alternatives
- Circular economy adoption
The future of silicone manufacturing continues to evolve with technological advances and increasing environmental consciousness. Manufacturers now combine traditional expertise with modern innovations to deliver superior products that meet specific industry requirements while maintaining sustainability standards.
Contact for further information: Phone: +1(647) 294-5240 Email: [email protected]
Related Articles
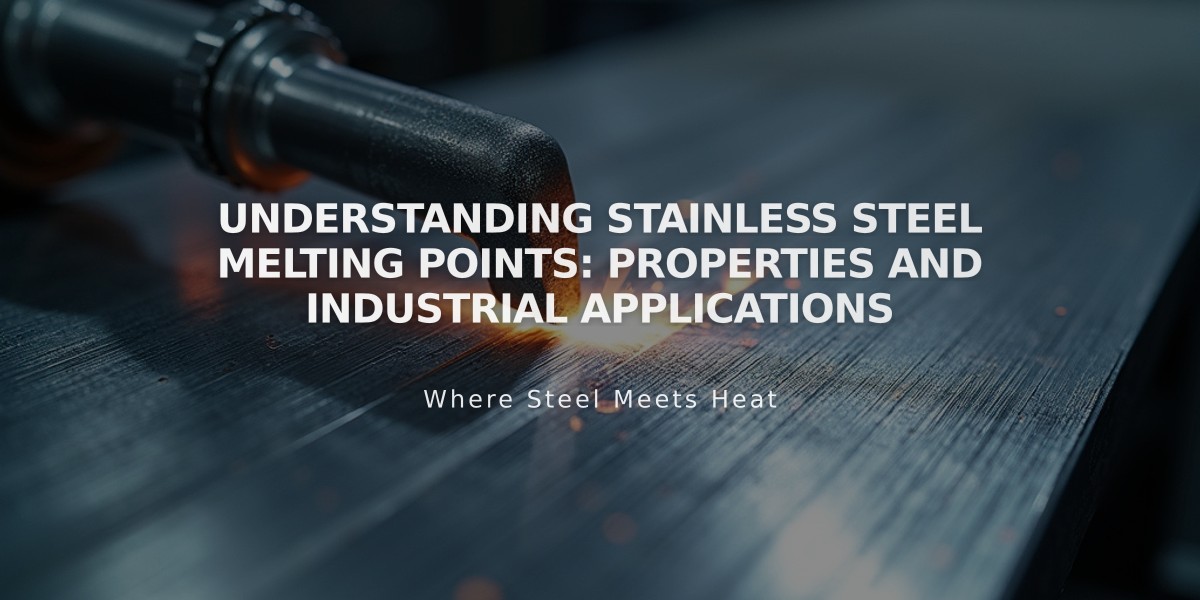
Understanding Stainless Steel Melting Points: Properties and Industrial Applications
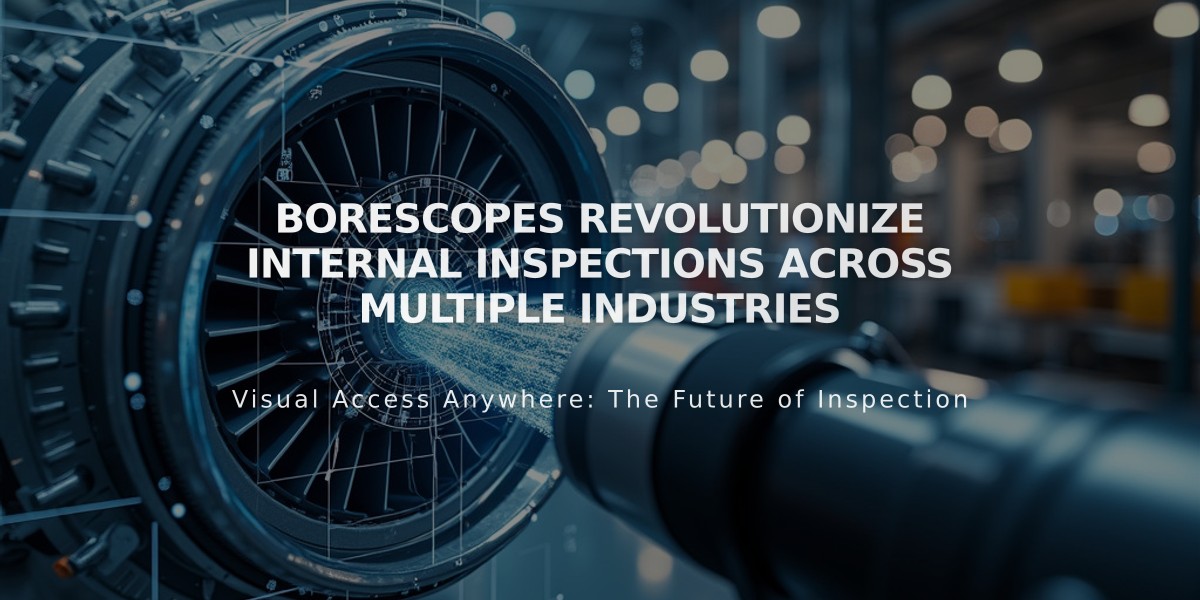