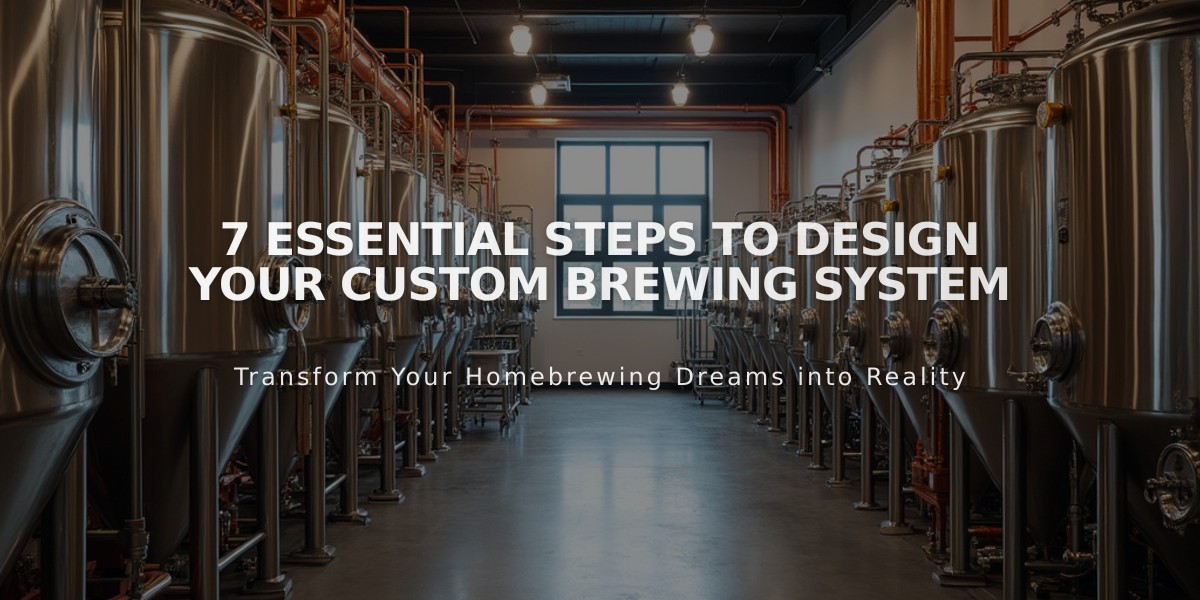
7 Essential Steps to Design Your Custom Brewing System
Starting a brewery requires careful planning of your brewing system. Here's a comprehensive guide to creating a custom setup that matches your needs and goals.
Determining Production Capacity
Before designing your system, calculate your desired annual output and batch sizes. Consider:
- Expected market demand
- Growth projections for 3-5 years
- Available space constraints
- Production frequency requirements
Brewhouse Configuration Elements
Key components to customize include:
- Mash tun size and design
- Kettle configuration
- Heat exchange systems
- Grain handling equipment
- Wort transfer methods
- Temperature control systems
Fermentation and Conditioning Setup
Essential factors for quality beer production:
- Tank sizes and quantities
- Temperature control capabilities
- Pressure handling requirements
- CIP (Clean-in-Place) systems
- Yeast management solutions
Automation Considerations
Choose your level of automation based on:
- Production volume
- Labor costs
- Quality control needs
- Recipe consistency requirements
- Budget constraints
Space Optimization
Efficient layout planning should address:
- Workflow optimization
- Safety requirements
- Equipment accessibility
- Future expansion possibilities
- Storage needs
Energy Efficiency Features
Implement sustainable solutions:
- Heat recovery systems
- Insulated vessels
- LED lighting
- Variable frequency drives
- Solar power options
Packaging Integration
Align your system with packaging needs:
- Kegging systems
- Bottling lines
- Canning equipment
- Storage solutions
- Distribution requirements
Quality Control Elements
Ensure consistent product quality with:
- In-line testing equipment
- Laboratory setup
- Sampling ports
- Monitoring systems
- Documentation procedures
A well-designed custom brewing system should balance efficiency, quality, and scalability while staying within budget constraints. Regular maintenance and updates will help maintain optimal performance as your brewery grows.